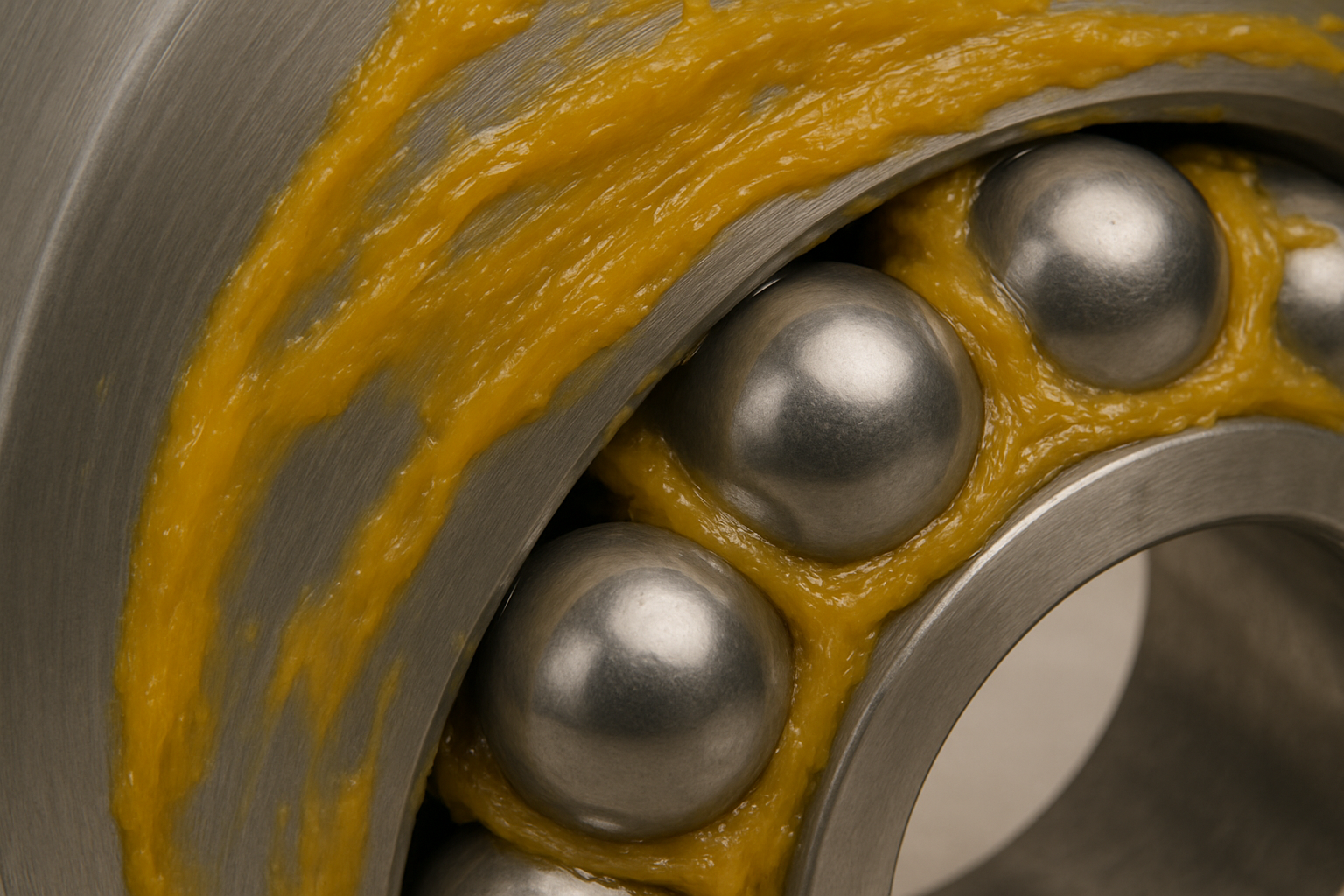
Behind every wind turbine failure category lies a complex web of failure modes, each requiring specific remediation strategies.
Consider grease lubrication failures in generator bearings—a seemingly standalone issue that actually represents a multifaceted challenge. Our data shows that grease-related failures fall into five distinct categories, each with different causes and solutions:
1. Grease Aging and Degradation: Exposure to high temperatures and oxygen causes oxidation. The base oil evaporates or polymerizes, leaving dry or hardened thickener, resulting in inadequate lubrication and rising friction.
As seen in the figure below (Figure-1), in one case, generator bearing temperatures are significantly deviating from the normal behavior range of that particular turbine.
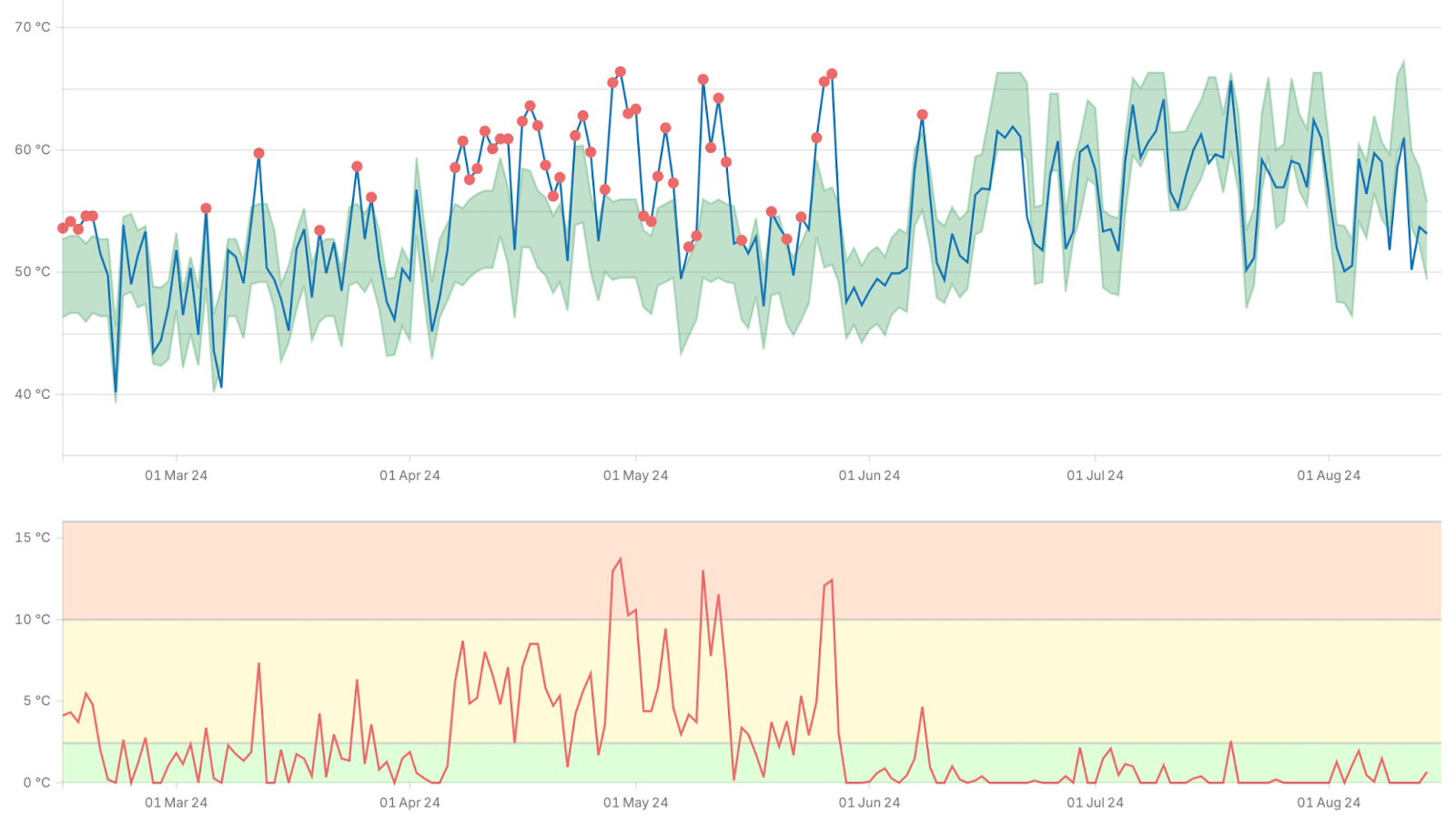
In another case, the oil became hardened, losing its lubrication quality entirely (Figure-2).
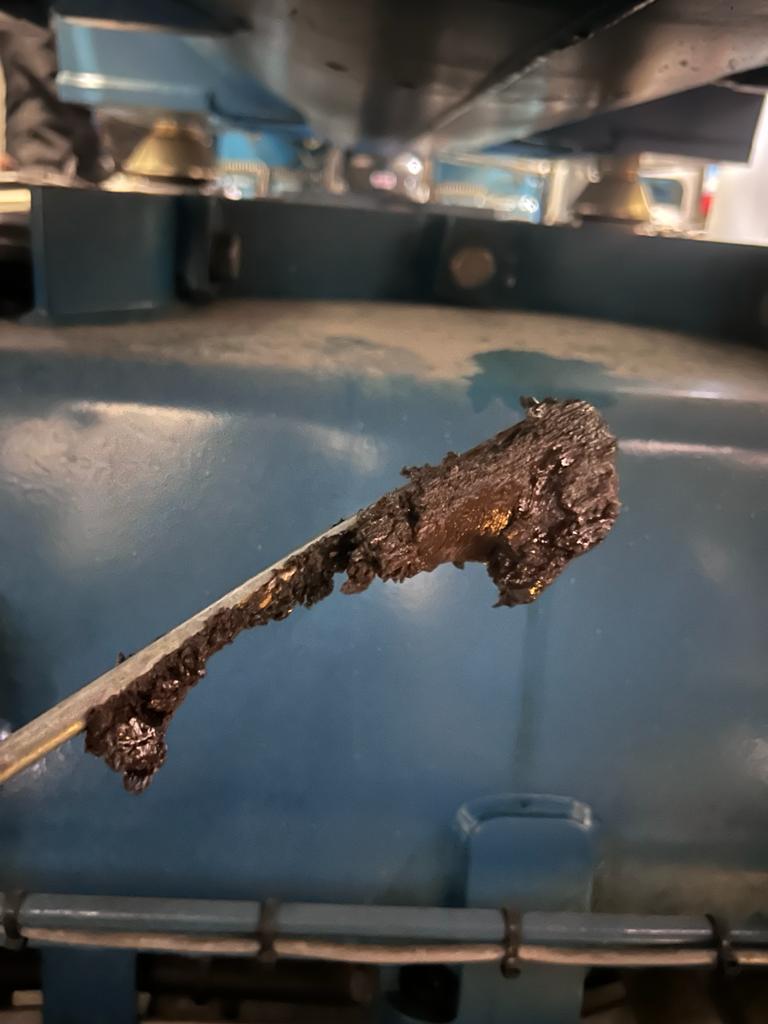
2. Under-Greasing: Too little grease leads to metal-on-metal contact. Occurs when grease intervals are missed or insufficiently applied.
3. Over-Greasing: Excessive grease causes churning, generating additional heat and resistance. Can also cause seal damage, allowing contaminants to enter.
4. Contamination: Ingress of dust, moisture, or salt can accelerate chemical degradation. Particulate matter creates abrasive wear inside the bearing, resulting in micro-pitting, spalling and reduced grease life.
In one case, contamination impacted both bearings in the front and back, eventually triggering power limitation and affecting the turbine's availability.
Another case created saponification (reaction between base oil and alkaline contaminants, e.g., water with metal ions or caustic residues, leads to soap-like deposits that thicken or harden the grease, resulting in increased resistance, reduced lubrication flow and potential bearing blockage).
In a third case, contamination reached significant levels requiring flushing as the only solution (Figure-3).
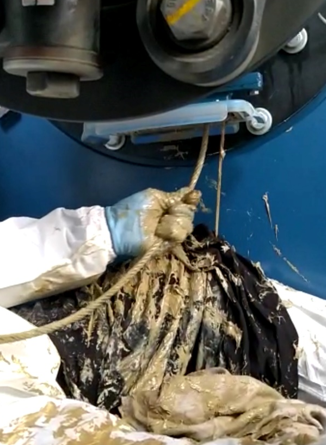
5. Grease Separation: In high-load environments, the thickener may fail to release oil consistently, resulting in starved lubrication despite apparent grease presence.
The Challenge of Root Cause Identification
While early detection of any failure, including grease lubrication ones, is already a challenge (unlike systems with real-time monitoring of lubricant condition, grease health is not continuously measured, making predictive failure detection difficult), guiding the asset owner and their O&M teams about the possible root cause is another beast, requiring extensive know-how of the machinery and corresponding malfunctions.
Without accurate root cause identification, maintenance teams are left guessing which remedial action to take. Is it time to replace the grease? Apply flushing? Change the seals? Each decision has cost implications and different effectiveness depending on the actual root cause. Even worse, a misperception of the root cause and a corresponding wrong action might make the problem worse and jeopardize the availability of the turbine.
The Kavaken Difference: Extensive Case Library
This is where Kavaken's extensive case library becomes invaluable. Our platform covers over 3 GW of wind assets across different turbine makes, types and ages in different terrains and environmental conditions. This diversity has allowed us to build a comprehensive database of failure modes and develop detailed subcategories of standalone failure types—such as the case with grease lubrication failures described above, which we've broken down into 5 detailed root causes.
When our Predictive Maintenance system detects an anomaly in a client's turbine, it doesn't just flag an issue—it also brings potential root causes to attention and enables the asset owner to focus on the right set of problems with remarkable accuracy.
Generator bearing grease lubrication failures represent just one category among thousands of potential failure modes in wind turbines. Each major component—from gearboxes to pitch systems—has its own complex taxonomy of failure types.
This complexity is why predictive maintenance technologies must evolve beyond anomaly detection. The complete value-add belongs to systems that not only identify that something is wrong but also specify what is wrong and why. Through our continuously growing case library derived from our worldwide portfolio, Kavaken provides this next level of insight—turning data into actionable maintenance decisions that prevent failures before they occur and optimize the lifetime of your wind assets.