Wind turbines are marvels of modern engineering, but like any complex machinery, they're susceptible to breakdowns. These breakdowns can be costly, causing downtime and lost energy production. This case study explores how Kavaken's Predictive Maintenance (PdM) module at a wind farm prevented a major issue by automatically detecting a malfunction in a turbine gearbox cooling system's thermal bypass valve.
The Challenge
In early 2023, a wind farm started experiencing a series of issues with one particular turbine. The most concerning symptom was abnormal oil temperature readings within the gearbox. Gearbox health is paramount for turbine performance, and excessive heat can lead to catastrophic failure.
Kavaken's PdM Steps In
Fortunately, the turbine was equipped with Kavaken's PdM module. This advanced system continuously monitors various turbine parameters obtained through SCADA (Supervisory Control and Data Acquisition) systems. These parameters typically encompass environmental and operational data such as wind speed, rotor shaft RPM, and ambient temperatures. The Kavaken platform uses sophisticated algorithms to analyze this SCADA data and identify anomalies that might signal impending problems.
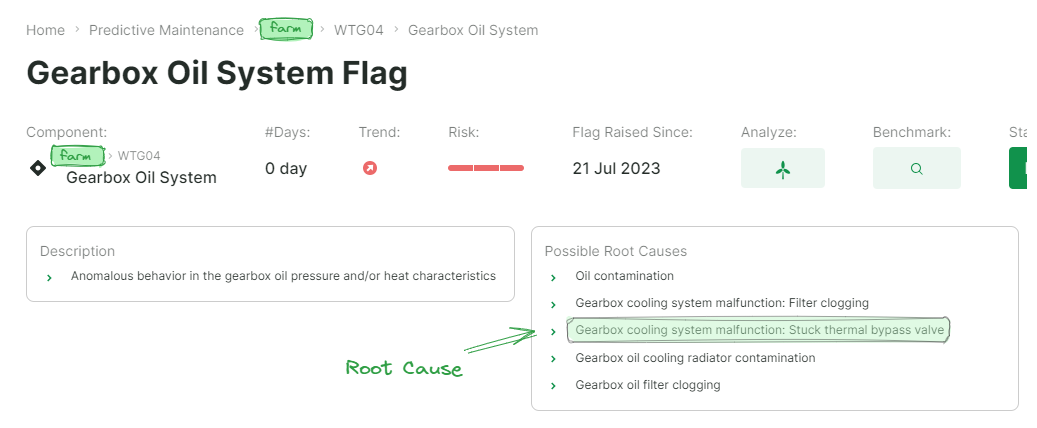
Here's a timeline of events captured by Kavaken's PdM module:
- July 21, 2023: The system flagged an initial anomaly and identified the thermal bypass valve as a potential root cause for the abnormal gearbox temperatures.
- September 26, 2023: Based on Kavaken's recommendation, the maintenance crew inspected the gearbox oil filter but found nothing unusual.
- December 4, 2023: Kavaken's early warning system continued to monitor the situation and informed the crew that the anomaly in all gearbox oil temperature parameters was still increasing.
- January 29, 2024: The maintenance team conducted an oil analysis, and the report did not reveal any abnormalities in the lubricant itself.
- February 22, 2024: Despite the oil analysis results, Kavaken's PdM system flagged a further increase in the anomaly level, stressing the urgency of investigating the thermal bypass valve.
- April 12, 2024: Prompting action based on Kavaken's persistent warnings, the crew finally checked the gearbox cooling system's thermal bypass valve. The inspection confirmed a malfunction, and the valve was promptly replaced.
.png)
Early Detection, Prompt Action
The faulty valve, crucial for regulating gearbox temperature, was not functioning correctly. This could have led to a significant temperature rise, potentially causing gearbox damage and extensive downtime. The swift action prevented a major breakdown, saving the wind farm significant costs associated with repairs, lost production, and potential grid penalties.
The Kavaken Advantage
This case study exemplifies the power of predictive maintenance in the wind energy industry. Kavaken's PdM module goes beyond simply monitoring data – it intelligently analyzes SCADA data to identify anomalies and predict potential failures. This empowers wind farm operators to:
- Proactive Maintenance: Address issues before they snowball into critical failures.
- Reduced Downtime: Minimize turbine downtime through early detection and repair.
- Optimized Costs: Avoid the high costs associated with major breakdowns and reactive maintenance.
- Improved Efficiency: Maintain optimal turbine performance for maximum energy production.
In conclusion, Kavaken's PdM module proved to be an invaluable asset for the wind farm. By automatically detecting a malfunction in the thermal bypass valve and providing crucial insights based on SCADA data, Kavaken helped prevent a costly breakdown and ensured the continued smooth operation of the wind turbine. As wind farms embrace ever-more sophisticated technology, PdM solutions like Kavaken will play an increasingly vital role in maximizing uptime, efficiency, and profitability.