In Part I of the series, we dug into the types of hydroelectric energy generating methods and turbines for different application purposes. Also mentioned are the mechanical and electrical components of hydroelectric power generation. This part will detail monitoring and predictive maintenance theory and practices of the hydroelectricity generating process and critical equipment.
Hydroelectric power generation plays a more vital role than ever in global power generation; thus, machine uptime, reliability and efficiency have become key factors in operational profitability. With the increasing demands on operations and maintenance (O&M) requirements, effective monitoring of these machines is of great importance.
The initial investment costs of hydropower plants are relatively high; however, they have a relatively longer lifespan than other energy plants. Typical average operations and maintenance costs for such plants are approximately 2% of the investment cost.
Preventive maintenance is mainly based on equipment historical time to failure averages and original equipment manufacturer (OEM) standards and thresholds are the most common method of maintaining hydropower plants. However, with the help of advancements in sensor technology, big data and machine learning, predictive maintenance finds more practical applications in the plants.
A predictive maintenance strategy optimizes the useful life of assets and resources to minimize operation and maintenance costs. The condition of equipment must be monitored regularly to implement predictive maintenance. Condition monitoring refers to the processes that enable early detection of machinery faults, failures and wear before they reach a secondary damage stage or catastrophic levels. The benefits of a condition monitoring program can be listed as follows:
- Extended asset life
- Minimized downtime and O&M costs
- Maximized production
- Better maintenance planning and logistics
- Reduced routine maintenance (preventive maintenance)
Early detection and diagnosis of faults maximize time to maintenance, ensuring optimum production, efficiency, uptime and reliability. Advanced measurement techniques, versatile database systems and well-established and trained predictive models help achieve accurate and reliable diagnosis and prognosis.
Data Sources
Hydropower plant equipment and processes generate vast amounts of data. Data sources will be investigated one by one in this section. In general, ultrasonic and vibration analyses tend to give earlier warnings than oil debris or SCADA trending analysis for rotating equipment. Stages of rotating equipment degradation are visualized in the PF(potential to functional failure) curve below:
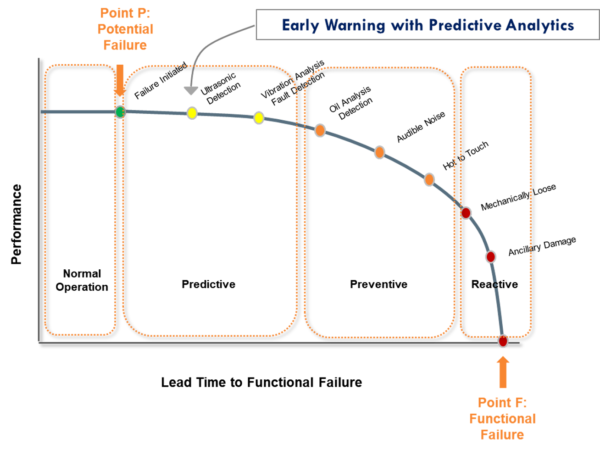
Let’s start with the vibration sensors, one of the most commonly used condition indicators of the rotating machines.
Vibration Measurement
Vibration data, when used appropriately, provide an early indication of most developing equipment faults; moreover, when associated with other data sources, it helps create more actionable fault management strategies.
For hydropower turbines, as with other rotating equipment, rotation speed, operating regime and load are among the factors that influence the vibration response. Today, it is compulsory that the working safety of machines and hydraulic turbines be protected against mechanical vibrations and their reliability must be high to ensure high availability. In addition to the raw acceleration, speed and displacement measurements; some modern condition monitoring systems (CMS) also calculate features like ISO (RMS of 10Hz-1kHz), high-frequency bandpass (HFBP), low-frequency crest factor (LFCF), vibration levels at various order of tooth meshing frequencies (TMF) and various order magnitudes of the shaft running speeds (e.g. 1MA, 2MA). Outputs of these filters and features are also useful for machine learning algorithms.
Usually, vibration measurements are recommended to be taken at the locations closest to the bearings. Sensors are mounted on each side of the generator bearings (drive end and non-drive end). Some applications include additional measurements on the rotor and shaft or concrete structure, foundation and the body. It is recommended to place accelerometers on the stators to identify possible structural problems in the core joints for large turbines. Depending on the turbine’s position (horizontal or vertical), displacement sensors are mounting angle changes.
ISO 7919-5:2005 norms for the peak to peak vibration ranges are usually used to compare vibration levels to the hydropower standards. The graph below shows that thresholds of the mentioned norms vary based on the machine's rotation speed (RPM).
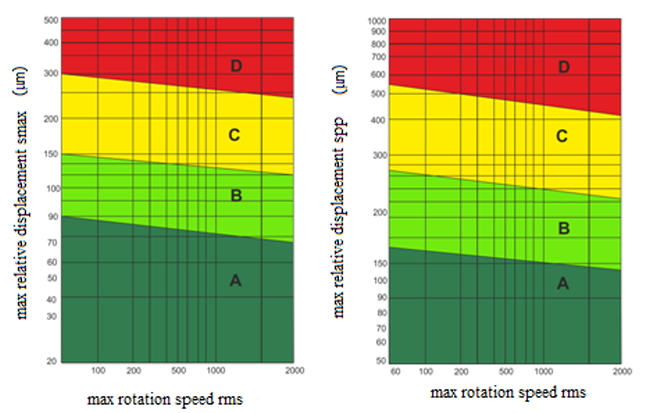
Process Data
Process data of hydropower plants is generally obtained from data acquisition systems called Supervisory Control and Data Acquisition (SCADA) which connect the turbines, the substation and meteorological stations to a central computer. The SCADA system, which the turbine supplier usually provides, keeps a record of all the activity (event logs, sensory measurements) on a 10-minute basis (10-minute average, min, max and standard deviation of 1 Hz sampled values) and allows the operator to determine what corrective action if any, needs to be taken.
SCADA data can be used for fault detection and diagnostic purposes too. Since the data sampling period is in a time interval of minutes, it is not appropriate for some conventional machine condition monitoring techniques, such as spectral analysis. Therefore, techniques for SCADA data analysis can be largely grouped into:
- Trending
- Clustering
- Normal Behavior Modeling (NBM)
- Damage Modeling
Trending is an arguably less complex method of analysis and it tends to be case-specific, requiring manual interpretation, or, if used online, generates frequent false alarms. Generally, trends are visually monitored and require human expertise to interpret the results.
Trending gearbox oil temperature against the produced power gives a curve (similar to the well-known power curve) that can be used to visualize gearbox efficiency drop. Also, trending generator bearing temperature against the produced power may indicate symptoms of a generator bearing degradation over time.
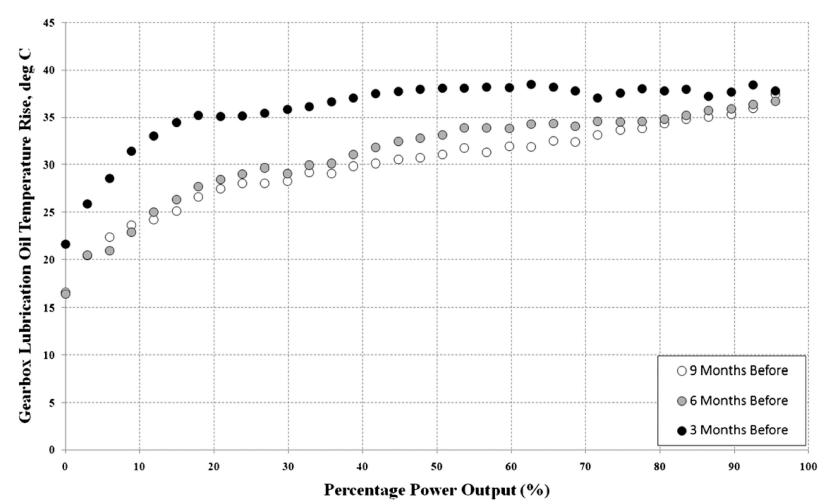
Clustering techniques like k-means, self-organizing maps, and DBSCAN are used to distinguish healthy and faulty data regions. These algorithms automatically learn to group healthy and faulty samples by utilizing the historical data used to classify new measurements for condition monitoring purposes.
NBM has become a popular approach to data analysis whereby a model for the normal behavior is established using historical training data, and the difference between predicted and actual values of the parameters is used for abnormality (fault) detection.
To establish an NBM model for a specific fault case, a SCADA parameter, say generator drive end bearing temperature, is selected as the “target”. Then, other relevant SCADA parameters to the target are determined using feature selection, reduction techniques, or plant expert opinions. Then a model between the relevant parameters to the target is established via regression techniques like linear/polynomial regression and artificial neural networks (ANN). In general, the temperatures of components are taken as “targets” to be modeled. NBM models, in addition to the exogenous inputs, can also take autoregressive parameters as input too. This means the previous timestamp of the “target” is also used for modeling the current target value. ARX, ARMAX, ARIMAX models are some of the known examples.
Different anomaly detection models can be used when comparing the outputs of the prediction models and the actual values, such as simple thresholds, Mahalanobis distance, or Shewhart control charts.
Damage modeling simply involves the implementation of physics of failure (PoF) models to calculate the damage or deterioration of the equipment. PoF models require expert knowledge of the equipment and physical principles of damage progression over time. It may be burdensome if not possible to model some failure modes. They are known to be very precise and accurate when done appropriately; however, they are costly compared to other approaches.
For instance, the Lundgren–Palmgren damage model is used for predicting gearbox bearing degradation alarming. The model constants are calibrated with the help of design lifetime and empirical lifetime tests. Sequential Monte Carlo simulations like Particle Filters are adapted into the modeling to estimate the remaining useful life of the equipment in practice. Paris Law is also used for modeling crack propagation of any metal surface fatigue.
Other specialized monitoring techniques which use other types of data sources are listed as follows:
- Partial discharge couplers for detecting partial discharge and stator winding insulation problems
- Air gap sensors for detecting generator air gap anomalies
- Magnetic flux meters are used for the detection of demagnetization of generators
- Three-phase voltage and current transducers are also used for electrical signature analysis
Types of Faults
Hydropower turbines are sensitive to numerous parameters that continuously reduce their lifetime. Mechanical forces, significant temperature differences, material destruction, cavitation, mechanical crushing, corrosion and chemical forces are some of the sources of various damage.
Over the past decades, many hydropower plants have switched from continuous baseload operation to periodic and partial load operation. Even though this periodic operation is considered more economical, it imposes an additional burden on plant equipment due to increased start/stop frequency.
The graph below summarizes the type of faults (top) and the root causes of electrical insulation system faults (bottom) in hydroelectric power plants. The most common failures are caused by the effects of aging and contamination of the winding by dust particles and moisture. Electrical failure mechanisms are also caused by internal partial discharges at the corona protection of the voltage grading and by high voltages. The vibration of parts may also cause loose bars and slot wedges of the stator.
The electrical insulation system (stator winding) plays the most critical role in the overall structure of a generator. Most failures occur in the electrical system and are caused by aging, electrical, thermal and mechanical load.
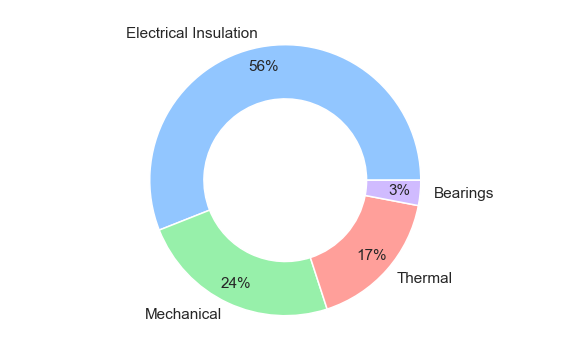
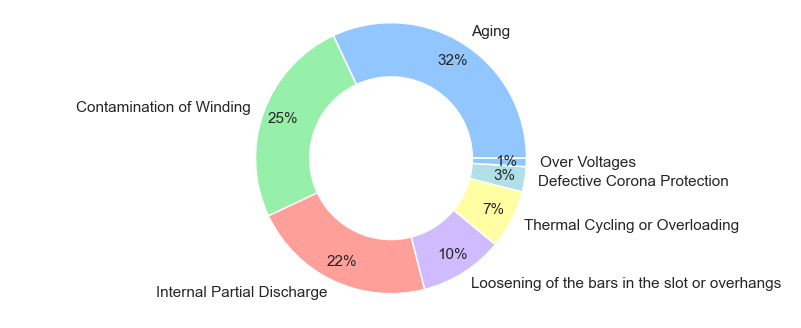
Misalignment and unbalance, looseness and deformations in the rotor ring, and changes in the pole positions are some of the known problems related to the rotor. Some examples are when it comes to the stator problems, decomposition of the stator core and frame, expansion of the concrete, and issues related to the anchor bolts.
Over time, expansion and formed cracks in the concrete material cause static eccentricity in the stator. Static eccentricity as a form of magnetic imbalance leads to an unevenly distributed air gap between the stator and rotor, increasing the excitation voltage.
Cavitation is considered one of the most critical faults that occur in hydraulic turbines. It is simply the formation of vapor cavities in water due to rapid changes in pressure. Cavities can grow, burst and emit large shock waves that cause pits at contact places. The cavitation phenomenon is critical in Francis turbines. Their runner blades are designed to have maximum efficiency for a given head and flow rate, so cavitation appears outside its design point. In Kaplan turbines, cavitation is less likely to occur as they can regulate the angle of their blades depending on the head and flow rate, which guarantees high performance throughout the operating range.
Some of the faults related to generator drive end (DE) and non-drive end (NDE) bearings and their cooling systems are as follows:
- Bearing overheating
- Insufficient heat transfer from the bearing cooling system
- Excessive bearing babbitt temperature
- Excessive lubrication oil consumption
Other problems can be listed as follows:
- Shaft imbalance
- Shaft seal ring degradation
- Excessive oscillations in the turbine area
- Excessive water pulsations in the water intake
- Insufficient heat exchange from oil/water heat exchangers
- Water consumption in the closed-loop system
- Performance degradation of the air pressure system
- Excessive oil consumption in the high-pressure unit
Data Analytics in Practice
In this section, we will give voice to what hydropower plant operators say; the problems they encounter in the plant, scheduled corrective action practices and how data analytics help in practice.
As the P-F curve suggests, it is highly likely to come across problems during the initial stages of operations, such as the commissioning of turbines. For instance, one of the runner blades may not move due to a loose bolt which is a manufacturing or commissioning mistake. If not monitored, problems may escalate and cause secondary problems and production loss. This could be detected by monitoring the vibration signals, which helps the maintenance crew prepare for torque tightening on time. Kavaken Predictive Maintenance module automates this process and provides plant personnel with a decision support system to achieve predictive maintenance. This is performed automatically by monitoring and predicting all relevant signals (including Vibration signals and SCADA measurements) in the plant with the help of big data technologies, machine learning and ever-growing domain expertise.
Let’s continue with the plant practices more. Usually, plant operators call a supervisor approximately every three years for hydraulic torque tightening of the bolts on the rigid side of the turbine to make sure the foundation of the turbine is not loose. The loose foundation phenomenon can be detected at early stages via automated use of electrical signature analysis or spectral domain analysis of vibration signals.
When river contamination accumulates on the radial gate filters, it creates a vortex. This could be detected by monitoring the vibration sensors, and the problem disappears following an appropriate filter clean operation.
Plant operators also mention that the radial gate hydraulic system tends to have aeration problems. Aeration occurs when air contaminates the hydraulic oil. Symptoms include erratic actuator movements, foaming of the oil, and a knocking or banging noise when it compresses and decompresses as it circulates through the system. This problem can be detected and its root causes can be found by monitoring the hydraulic system and its close encounter measurements.
It is known that failures occur less frequently in hydropower plants compared to wind farms due to the short maintenance and part replacement cycles and lower turbine rotation speeds. Their part replacement and maintenance schedules are also tight, contributing to high costs due to unnecessary parts replacement and maintenance and production loss due to downtimes.
What does Kavaken Offer?
Kavaken’s Predictive Maintenance modules bring the data science and machine learning expertise in the predictive maintenance and condition monitoring of hydropower turbines, generators and other auxiliary equipment in the plant. The module employs an ensemble of standard behavior models and multivariate anomaly detection models with a smart integration and thresholding mechanism to produce accurate and precise fault alarms. Fault alarms are displayed on the platform’s specific pages and notifications are sent to plant operators and engineers.